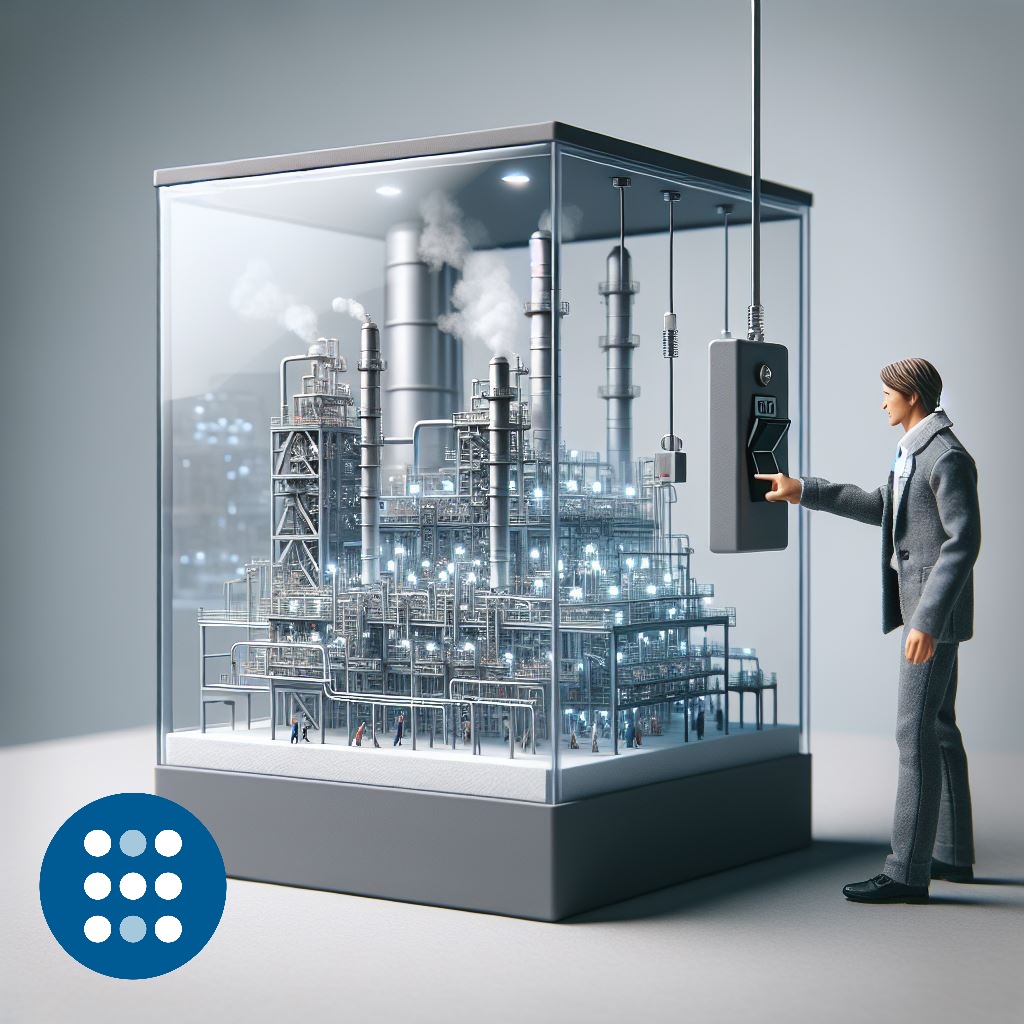
-
Small-scale steam reforming offers a versatile and scalable solution for meeting localized hydrogen production needs and will play a crucial role in shaping the future of hydrogen generation.
-
The integration of precious metal catalysts and catalysed hardware are key enablers for a small-scale steam reforming process.
-
At Hulteberg we have the catalysis expertise and will continue to support the development.
In the evolving landscape of energy production, small-scale steam reforming is a viable and efficient method for generating hydrogen, hydrogen that can be subsequently used in fuel cells. This process offers a promising solution for meeting localized hydrogen generation needs. The integration of precious metal catalysts and catalysed hardware has significantly enhanced the efficiency and practicality of small-scale steam reforming, making it an attractive option for various applications, in particular to power data centres. At Hulteberg, we have worked with catalysed hardware and the highly active catalysts that needs to go with it for decades.
Small-Scale Steam Reforming
Small-scale steam reforming is a process where hydrocarbons, such as natural gas, react with steam at high temperatures in the presence of a catalyst to produce hydrogen, carbon monoxide and carbon dioxide. This method is particularly advantageous for producing hydrogen on-site and on-demand, reducing the reliance on large-scale hydrogen production and hydrogen distribution networks. Small-scale steam reforming units can be deployed in diverse settings, from small industrial plants, e.g. in glass production, to fuelling stations, providing flexibility and convenience in hydrogen generation.
Precious metal catalysts
Precious metals, such as rhodium and platinum, play a crucial role in enhancing the efficiency of the steam reforming process and its catalysts. These catalysts offer several benefits, first of all, precious metals exhibit exceptional catalytic activity, which translates to higher conversion rates of hydrocarbons, potentially resulting in smaller reactors. Secondly, precious metal catalysts are known for their durability and stability under the harsh conditions of steam reforming. This longevity ensures consistent performance over extended periods, reducing the need for frequent catalyst replacement and maintenance. Finally. hydrocarbon feedstocks often contain impurities that can poison catalysts, such as sulphur, diminishing their effectiveness. Precious metal catalysts exhibit a remarkable resistance to poisoning, maintaining their activity even in the presence of contaminants. As a bonus feature, this class of catalysts are not severely impacted by oxygen. This means that it is not problematic to have trace amounts of oxygen in the feed, or indeed, to have oxygen reach the catalyst during stand-still, something that is not feasible with traditional, nickel-based catalysts.
Catalysed hardware
In addition to precious metal catalysts, advancements in catalysed hardware have further optimized the small-scale steam reforming process. Catalysed hardware, such as fins, heat exchangers, filters and microchannel reactors, offer several advantages. Catalysed hardware is, for instance, designed to improve heat and mass transfer within the reactor, ensuring uniform temperature distribution and efficient contact between the reactants and the catalyst. This optimization enhances the overall efficiency of the reforming process and maximizes hydrogen space yield. A good approach to catalysed hardware features compact and modular designs, making it easier to integrate into various applications and settings. These units can be scaled up or down based on the specific hydrogen generation requirements, providing flexibility and adaptability, but also combine unit operations such as heat exchanging and filtering with catalysis.
Hydrogen
To conclude, the integration of precious metal catalysts and catalysed hardware has the potential to revolutionize small-scale steam reforming, making it a highly efficient and practical method for hydrogen generation; a revolution already started. The high activity, durability, and resistance to poisoning of precious metal catalysts, combined with the advancements in catalysed hardware, have significantly enhanced the performance and reliability of small-scale steam reforming units.
As the demand for hydrogen continues to grow, small-scale steam reforming offers a versatile and scalable solution for meeting localized hydrogen production needs. Its applications in industrial settings, fuelling stations, and remote locations highlight its potential to support the transition to a sustainable and hydrogen-based energy future. By continuing to innovate and optimize the process, small-scale steam reforming will play a crucial role in shaping the future of hydrogen generation and contributing to a cleaner and more sustainable world, and Hulteberg will continue to support the development.